Revolutionizing Sustainable Construction with GFRC As the construction industry increasingly prioritizes sustainability, innovative materials like GFRC panels are taking center…
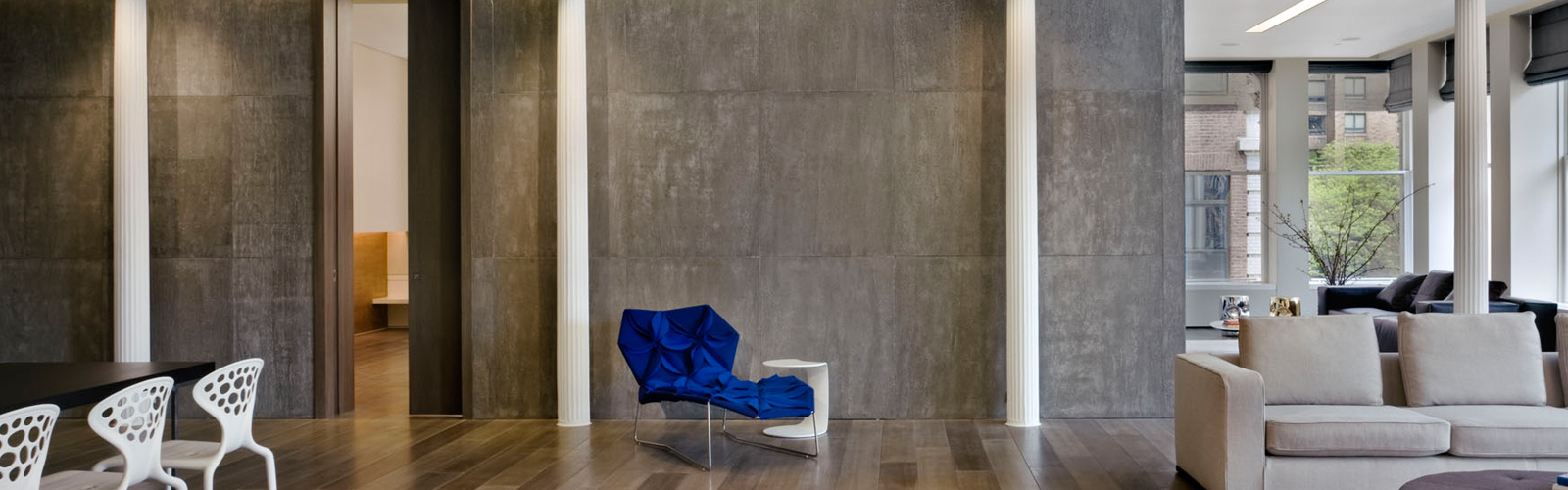
One of the top questions we get from people is about how we make our precast concrete panels. We are happy to take you through the process so you can understand your project from start to finish.
We start by collaborating with you, and the project’s architect and contractor, on producing a set of fabrication drawings. If engineering is required, as is typical with exterior cladding applications, we will work with an engineer to confirm attachment design. Once the design is coordinated amongst trades and approved, we finalize those plans and begin making the molds. We often use a variety of plywood or engineered boards to make the molds, usually determined by the size and quantity of panels. The molds need to be moisture-proof so that the moisture from the concrete does not warp it. Any mistakes at this step would result in panels that are out of spec, so molds are sealed at all seams.
Sometimes, we need to have a more shapeable mold, especially if your design has a specific aesthetic such as 3-dimensional patterns or textures.. To create those, we often use custom formliners. The form liners could be rubber, plastic, foam, or similar materials. We use a CNC machine or hot wire cutter to cut the foam to create shapes in which we use to create patterns or other decorations on the panel. The nature and type of formliner can impact the cost of the project—rubber is often reusable, while other materials are not.
Once the molds are complete, we prepare for casting the panels. We begin mixing the concrete. We handle all of our own aggregate mixing to ensure that the product is perfect for your project. Glass Fiber Reinforced Concrete (GFRC) is a combination of Portland cement, fine aggregate, polymers, glass fiber strands, and water. You can learn more about the GFRC mix matrix here.
Pigments are also added during mixing to produce your panel’s chosen color. We can customize every project to give you almost unlimited combinations of finish or color. Once we have it mixed, the concrete is ready to be poured.
Depending on the application, the GFRC mix may either be directly poured into the molds, known as a direct cast, or a face mix, which is void of fibers, is sprayed onto the forms first prior to the direct cast. The advantage of spraying a face mix layer is for color consistency for large surface area castings. During the pour, glass fiber mesh scrim is added to the panels for additional structural strength. The molds are screed at the end of casting for a smooth, level backside to the panel. GFRC panels will cure for demolding in 16-24 hours.
The panels will cure for an additional day before entering the finishing process where, depending on the chosen finish, will be wet polished, acid etched, or washed, before a protective sealer is applied. The panels and sealer will cure for an additional 3-7 days, then finally the panels are packaged into custom built crates so your panels arrive at your job site any where in the country safe and sound.