In modern construction, fire safety is a critical consideration when selecting building materials, particularly for exterior wall surfaces and cladding…
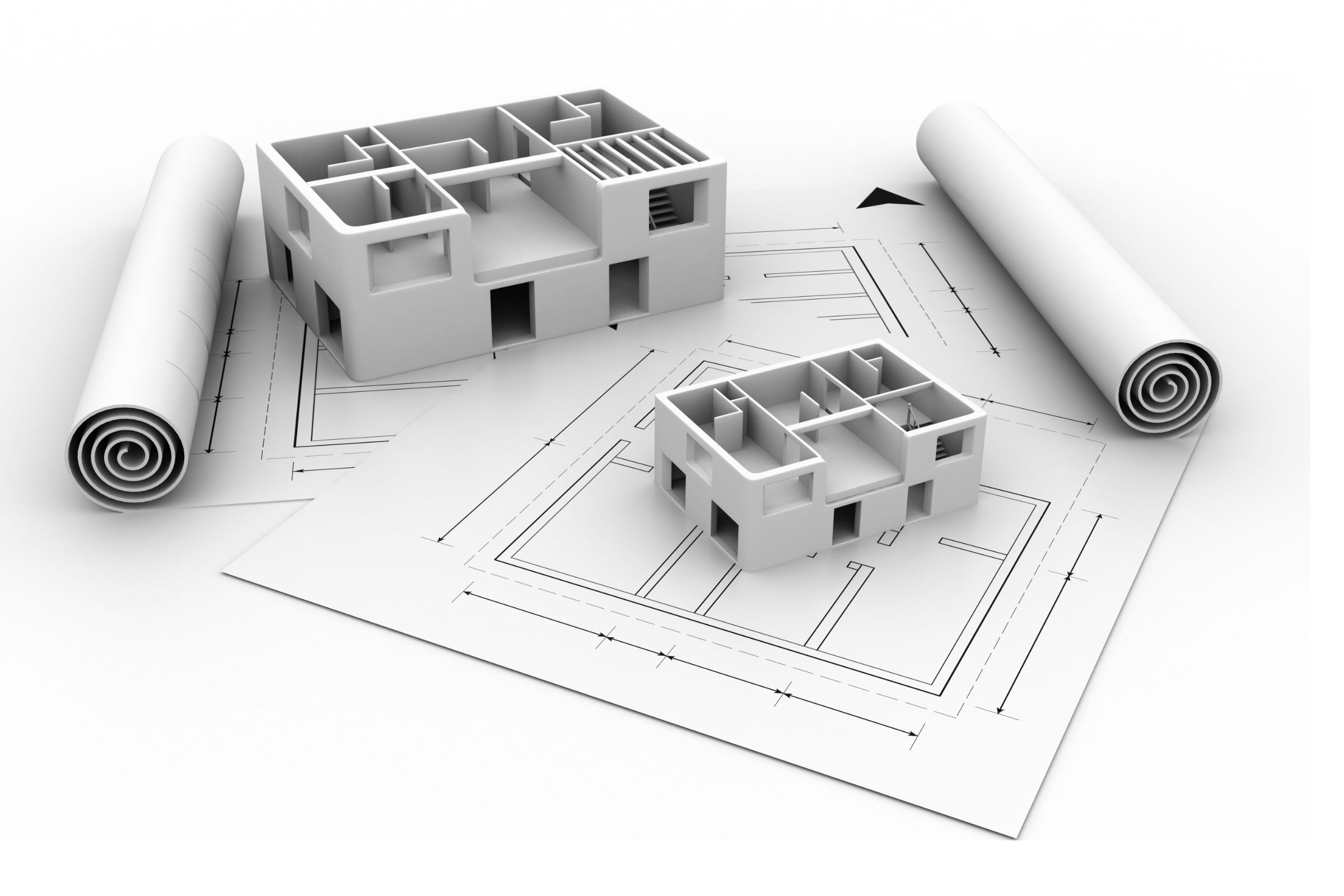
Reinforced concrete has been a cornerstone of architectural innovation for over a century. Originally designed by French gardener Joseph Monier to create imaginative landscape features, it has since evolved into a critical element of modern architecture.
In recent years, the construction industry has witnessed a surge in new technologies that are reshaping traditional building methods. While 3D concrete printing has garnered a lot of attention as a cutting-edge innovation, it’s not always the most practical or relevant solution for every construction need. 3D mold making, a more precise and adaptable technique, is emerging as a key player in the world of concrete fabrication.
What is 3D Mold Making for Concrete?
3D mold making involves using advanced digital modeling tools to create custom molds that can then be used for concrete casting. Unlike 3D concrete printing, which layers concrete to form a structure, mold making focuses on creating intricate, reusable forms for concrete, allowing for consistent quality and design flexibility. This method is particularly valuable for architectural features, custom components, and high-detail elements like facade panels or ornamental structures.
The Limits of 3D Concrete Printing
While 3D concrete printing has captured headlines, it’s important to acknowledge its limitations, especially when considering its practicality in large-scale or detailed projects.
Surface Finish and Detailing:
3D concrete printing struggles with achieving fine surface details and high-quality finishes. The layered approach can leave visible striations that may not meet the standards required for detailed architectural projects.
Material Constraints:
The types of concrete used in 3D printing are often restricted, limiting the potential for more durable or specialized mixes that may be better suited for long-term construction.
Reinforcement Challenges:
While some 3D printers allow for basic reinforcement during the printing process, they are still far from the level of reinforcement that traditional mold-based methods can provide. This limits their application for projects requiring strong structural integrity.
Job Impact and Skill Requirements:
The rise of automation in construction raises concerns about job displacement in the industry. While 3D printing aims to reduce labor needs, it also risks sidelining skilled tradespeople who are essential for maintaining quality and craftsmanship.
Why 3D Mold Making is a Superior Choice
In contrast to 3D concrete printing, 3D mold making offers significant benefits that align more closely with the requirements of modern construction:
Precision and Detail:
Molds allow for highly accurate and detailed designs, ensuring that complex architectural features are reproduced with precision. This is crucial for decorative elements and bespoke projects.
Versatility of Materials:
Unlike the limited concrete mixes used in 3D printing, mold making supports a wider range of materials, offering flexibility for projects that demand specific performance characteristics like increased durability or weather resistance.
Consistency and Reusability:
Once a mold is created, it can be reused for multiple projects, ensuring consistency in quality and reducing overall costs. This makes it an ideal choice for large-scale developments where uniformity is key.
Faster Production with Higher Quality:
While 3D concrete printing is often marketed for its speed, it can’t compete with the efficiency of casting from 3D molds when it comes to delivering both speed and superior craftsmanship. Mold making supports faster production while maintaining high standards for surface finish and structural integrity.
Conclusion: The Path Forward
Although 3D concrete printing continues to be a buzzworthy topic in the construction world, it’s clear that 3D mold making offers a more reliable, flexible, and practical solution for many concrete fabrication needs. By focusing on precision, material versatility, and quality, mold making aligns with the demands of modern architecture while avoiding some of the downsides associated with 3D printing technology.
For architectural projects requiring high detail, consistency, and durability, 3D mold making is the future of concrete fabrication.